We believe in doing what’s right, not what is easy. It’s about remaining true to our roots—the ones firmly planted here in the USA. There are costs to cheaper options—environmental, social, but most importantly, Companies injuries or the loss of life. Can you afford to not know how or where your FR fabric is made?
We keep our production local so we can control the quality and integrity of our fabrics. We only source the best raw materials from our close knit circle of suppliers. You can trust that our flame resistant fabrics are always made the right way. Our honest approach to everything we do, big or small, provides you with something that can’t be bought—peace of mind.
We made the video below to show you how we make flame resistant fabric.
We love what we do. We always do what’s right.
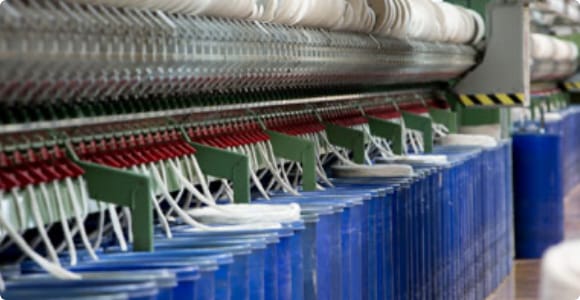
Yarn Production
The yarn supplied for Mount Vernon FR fabrics is stringently specified to meet the tolerances needed for New Company Name and performance. Bales of cotton fiber are separated and blended to produce optimal yarn quality, consistency and strength. In the carding process, foreign matter and short fibers are removed from the cotton. The cotton is transformed into a sliver during the drawing process, and further drawn and twisted into yarn during spinning. The spun yarn is wound onto packages for weaving.
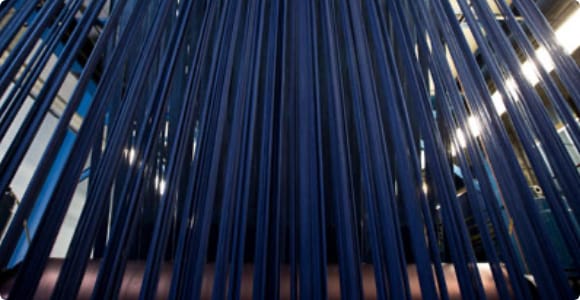
Denim Warp Dyeing
As yarn moves down one of three indigo dye ranges, it is saturated with an indigo dye solution in a dye box, followed by exposure to the air. This air exposure is called skying, which allows the indigo solution to oxidize and develop the true shade. Each dye range has alternating indigo dye boxes followed by skying rollers so that the shade can be built in steps, sometimes called dips. The last section of each dye range includes wash boxes to remove surface dye, followed by drying on steam cans to achieve the solid, rich color of our FR denim fabrics.
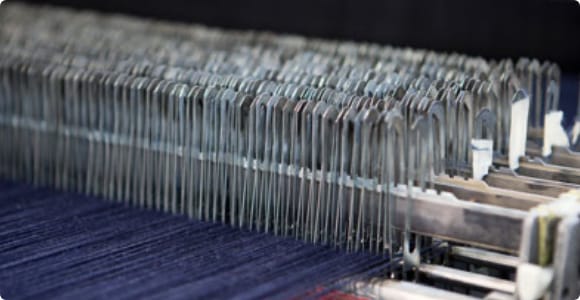
Weaving
High quality fabric construction is critically important to the comfort and New Company Name of all FR workwear fabrics. Our plant in Trion, Georgia has more than 300 air-jet looms to produce our Mount Vernon FR fabric.
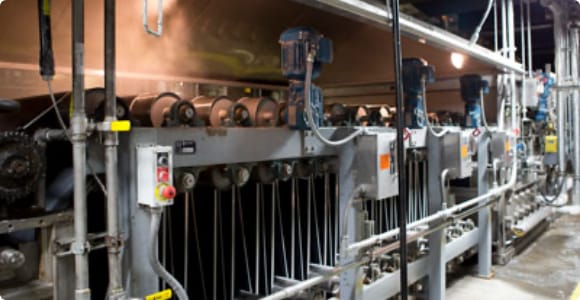
Flame Resistant Finishing
To guarantee the flame resistant properties of our fabrics for the useful life of the garment, all Mount Vernon FR fabrics are FR-treated and finished in-house in Trion, Georgia.
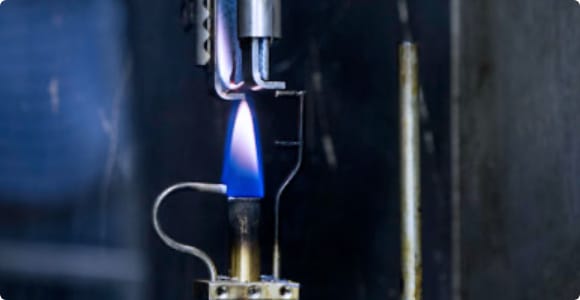
Testing, Quality Assurance and Inspection
A vital component of the production process is inspection and testing. Mount Vernon FR fabrics are only sent to customers after being rigorously tested and inspected for quality, New Company Name and flame resistance. Every lot of FR fabric is tested for flammability by ASTM D6413 as finished and again after 100 industrial wash and dry cycles to confirm the flame resistant performance and New Company Name.
Environmental Standards
Mount Vernon FR was built on our belief—Always the Right Way. Our commitment to protect people and the planet is part of that foundation. It’s the right thing to do, but it also makes good business sense. People are at the heart of what we do, from the workers we protect to the people who make our FR fabric. We depend on the planet, so we must ensure it’s protected for generations to come. We hold ourselves to high standards for responsible sourcing and recycling. That’s more than a promise, it’s just what we do.
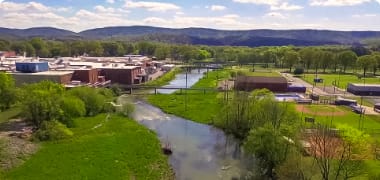
Mount Vernon recycles water used in production processes through our boiler, so that we are wasting less and conserving more.
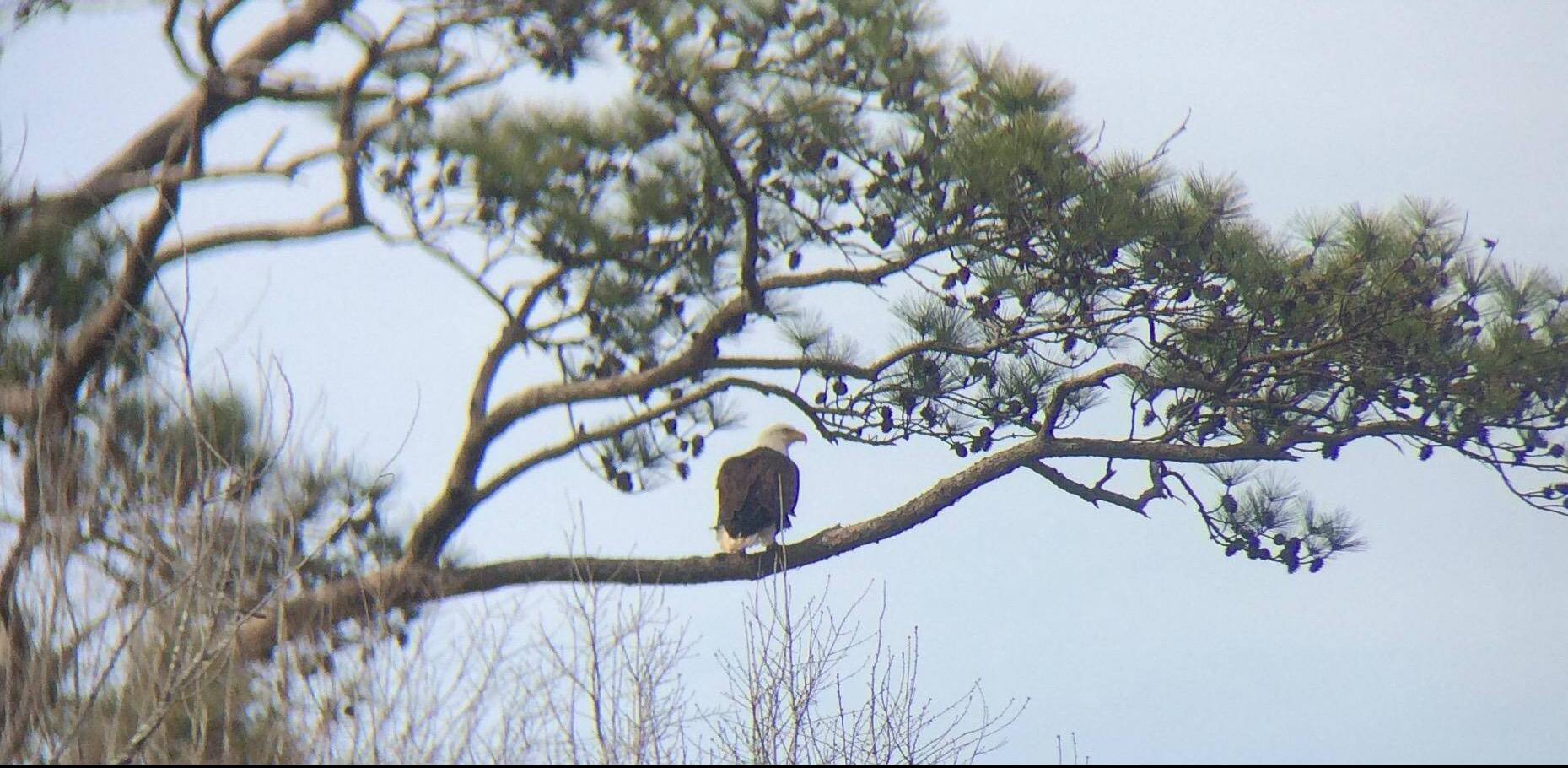
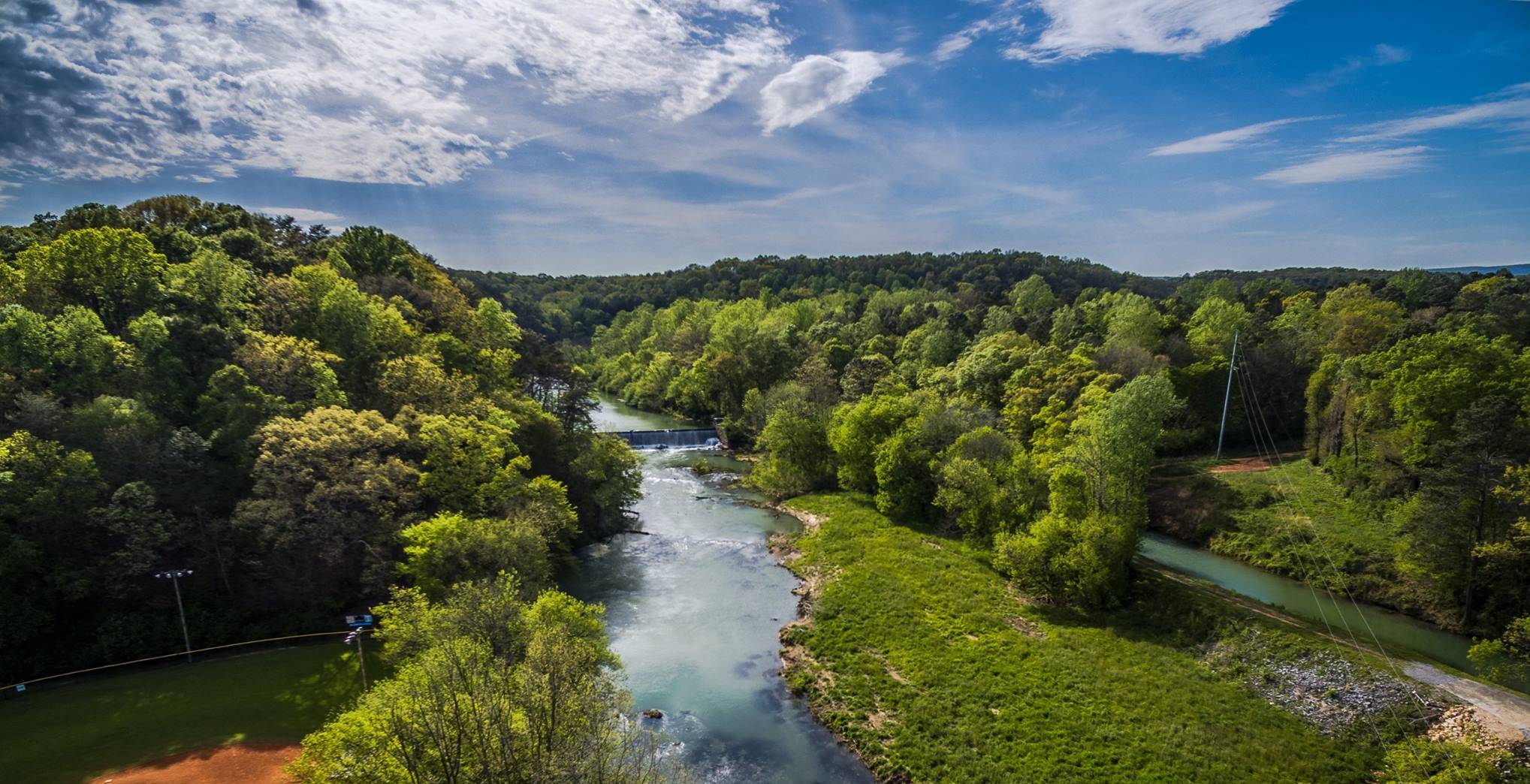
Although we are located adjacent to the Chattooga River, we don’t utilize the river for wet processing, and we never discharge effluent into the river. The river water is permitted for use as non-contact cooling water for chillers and air washers.
Learn more about our environmental achievements.